The Crystal Art.
The
revolutionary discovery that crystal could be insufflated and expanded
to any shape was made in the third quarter of the 1st century BC, in the
Middle East along the Phoenician coast.
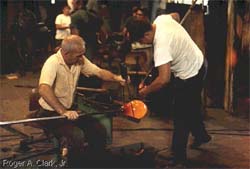
Crystalblowing
soon spread and became the standard way of shaping crystal vessels until
the 19th century. The necessary tool is a hollow iron pipe about 1.2 m
(about 4 ft) long with a mouthpiece at one end. The crystalblower, or
gaffer, collects a small amount of molten crystal, called a gather, on
the end of the blowpipe and rolls it against a paddle or metal plate to
shape its exterior (marvering) and to cool it slightly.
The
gaffer then blows into the pipe, expanding the gather into a bubble, or
parison. By constantly reheating at the furnace opening, by blowing and
marvering, the gaffer controls the form and thickness. Simple hand tools
such as shears, tongs (pucellas), and paddles are used to refine the form,
often while the crystalblower
sits in the special "crystalmaker's chair," one with extended
arms to support the blowpipe. Blown crystal can also be shaped with molds:
Part-size molds pattern the gather, which is then removed and blown to
the desired size.
Full-size
molds into which the gather is entirely blown impart size, shape, and
decoration. Additional gathers may be applied and manipulated to form
stems, handles, and feet, or they may be trailed on and tooled for decoration.
A shaped bubble can be "flashed" with color by dipping it into
molten crystal of contrasting color. To make cased crystal, a gather is
placed within, and fused to, one or more layers of differently colored
crystal. For finish work and fire polishing at the mouth of the furnace,
the gather is transferred to a solid iron rod called a pontil, applied
opposite the blowpipe, which is then removed. When the pontil is cracked
off it leaves a "pontil mark" that may be later ground or polished
away.
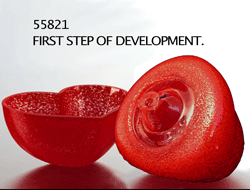
|